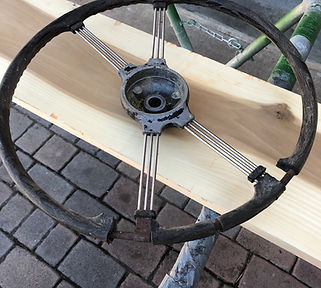
I have an old MGA steering wheel that I'm going to rebuild with a wood covering around the internal metal frame. The original MGA steering wheel was built with a hard rubber coating that shrinks and cracks over time. I've tried one of the rebuild kits and the results look good until you put the wheel on the car and actually use it. Basically the cracks come back. This is the second wheel that I'm rebuilding and I'll make this one a lot thinner than the first one.
​
I just put this wheel in the vice and started removing the old covering with a set of channel locks. This process takes 10 minutes.
I start the project with an eight foot clear popular board that has some character in the grain. The board is cut into four pieces and glued two of them together using Elmer's Wood Glue. I did the same for the other two pieces. Regular wood clamps were used to hold everything together for 48 hours.


I drew an outline of the wheel on the boards and added a half inch around the outside and inside of the outline. This is easy to do with a pencil and a piece of wire. Here you can see the outline of the wheel rim and the half inch added to the top and the bottom.
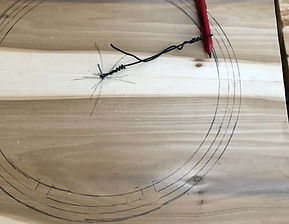
Once I had the basic design laid out I highlighted the areas that needed to be routed out and dug out the area that the steering wheel ring would sit in. I did this with a router but I think the job could be done better with a set of wood chisels. The router did not give me the control that would have made for a much smoother cut. This was done on both boards and each cut was about on half the width of the outside ring.


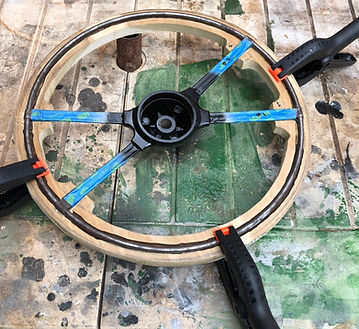
I used a regular saber saw with a fine blade to cut out the outside first and then the inside.

After all the sawing was completed I spent some time fitting the wheel to the top and bottom pieces. Be sure to label which piece is the top and which is the bottom because the bottom piece will need deeper groves to account for the angle of the arms. You will probably need some additional shaping to make everything fit at this point.
​
Both halves should fit together with no gaps between them.
I used a marine gel epoxy to hold everything together. I found this one at a boat store but I'm sure Home Depot or a hardware store will have something similar. I mixed up a good batch of epoxy and filled in the voids in both the top and the bottom pieces. This brand of epoxy works very slowly so you do not have to rush to get things clamped together.

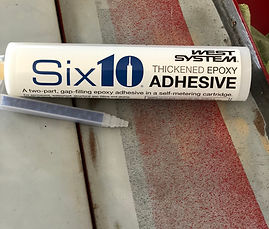
I clamped everything together with every clamp I had in the garage and If I'd had a couple of extra I would have used them.
​
Once everything is clamped use an air tool to blow away the excess epoxy. I didn't do this when I had the chance and it created extra work.